Switch to Intelligent Switchgears
- Switchgears
- May 1, 2020
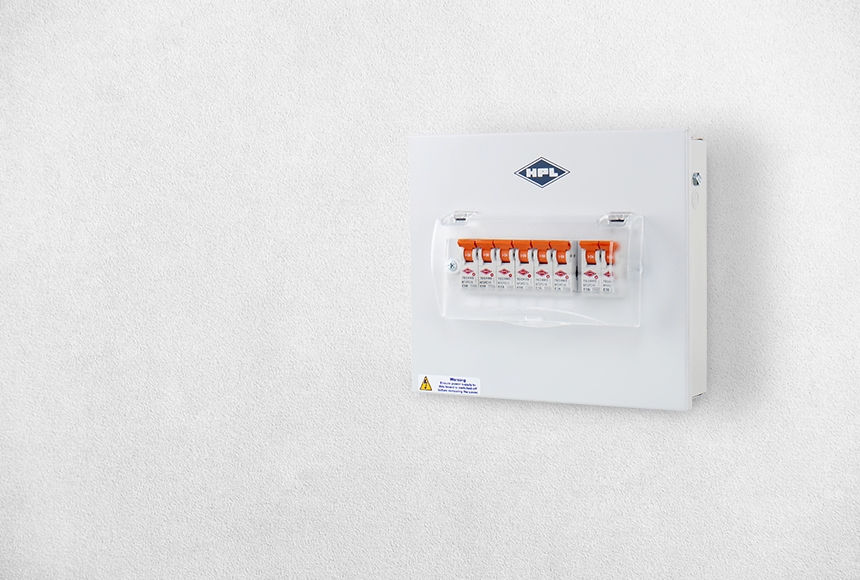
Internet of Things (IoT) is transforming every other industry and like every other industry, power sector too is going through a sea of changes, revolutionizing nearly every part of the industry from the transmission, generation to distribution, changing how consumers and electrical manufacturing companies interact. Nowadays, the switchgear is turning inherently intelligent, powered and connected by software-enabled solutions, mso-data-placement same-cell intelligent switchgear mso-data- placement:same-cell intelligent switchgearallowing a way to predict their maintenance.
To describe it in simple words, smart and intelligent switchgear is a power distribution solution programmed to self-monitor and manage electricity usage and reduce costs. The technology has enabled in producing such products which are pre-programmed for remote monitoring and communication enhancing protection, monitoring and control. Moreover, by utilizing efficient internal computer technology, intelligent switchgear can overcome the disadvantages of common electric switchgear to perform functions as electric fire prediction prevention, system diagnosis and electric power demand prediction. Switchgears can also identify patterns and predict failures in advance. Hence, minimizing the failures and downtime.
Intelligent Switchgears are better than normal switchgear as they have:
Upgraded breakers with modern-day communication and other power monitoring technology, instead of existing circuit breakers that offer trip units.
By installing thermal sensors to plan ahead and avoid any possible issues due to degradation of the material or any maintenance required.
By installing a partial discharge monitor which enables the customers to remotely monitor the degradation of insulation material or any issues contributing too many arc flash incidents.
With smart relay auto-transfer systems, you can control possible arc flash incident energy and maintain voltage in the front of the switchgear.
Upgrading existing buildings to comply with new safety expectations and regulations.
Over recent years, the emergence of several technological solutions has significantly enhanced the efficiency of operational utilities and made projects more viable by scaling down costs. With user interfaces getting IoT enabled and the devices getting smarter, intelligent switchgear is catering to the need for centralized control enabled by intelligent switchgear for smart cities which makes the Intelligent Switchgear the next big trend.
Enquire Now
Category
Post
-
Avoid These Common Errors While Operating Changeover Switches24 Jul 2025
-
Top 6 Electrical Wiring Challenges & How to Tackle Them Safely21 Jul 2025
-
Why Choosing the Right Electrical Equipment Matters for Builders09 Jun 2025
-
Importance of Fire-Retardant Modular Switches For Home26 May 2025
-
The Aesthetic and Functional Excellence of HPL's Modular Switches17 May 2025
-
Understanding Switchgear & Its Applications14 May 2025
-
5 Safety & Compliance Essentials for Modular Switches And Sockets in Industrial Setups14 May 2025
-
How to Choose the Right Changeover Switch for Industrial Applications02 May 2025
-
How to Choose the Right MCB: Tips by the Best Electrical Company In India14 Apr 2025
-
Key Advantages of Modular Switches11 Apr 2025
-
HPL Electric: Powering India’s Growth with Cutting-Edge Electrical Solutions05 Apr 2025
-
The Role of Changeover Switches in Backup Power Systems01 Apr 2025
-
Smart Switchgear for Smart Cities: The Role of Indian Manufacturers08 Jan 2025
-
The Backbone of India's Energy Sector: Key Electrical Equipment and Innovations08 Jan 2025
-
How Modular Switches Enhance Safety and Aesthetics in Modern Homes17 Dec 2024
-
Top Features to Consider In The Best Electrical Modular Switches For Home17 Dec 2024
-
Tips and Measures: Protect your home from electrical disasters26 Sep 2024
-
How does MCB changeover work?12 Sep 2024
-
4 Warning signs to know if your power socket needs an upgrade19 Jul 2024
-
What is a changeover switch? - Hpl electric & power ltd08 Apr 2024
-
What is the modular switch?- Hpl electric & power ltd06 Apr 2024
-
What is Digital Meter? - Hpl electric & power ltd18 Jan 2024
-
What is a Changeover switch? - Hpl electric & power ltd05 Jan 2024
-
Commercial LED Spotlights - HPL Electric & Power Ltd13 Dec 2023
-
What is Instrumentation Cable09 Dec 2023
-
What are the advantages of telephone cables? - Hpl electric & power ltd14 Nov 2023
-
What is Industrial Switchgear? - Hpl electric & power ltd10 Nov 2023
-
Instrumentation cable manufacturers - Hpl India24 Oct 2023
-
What is Digital Panel Meters? - Hpl India19 Oct 2023
-
How Special Cables Make Wiring Safer and Effective12 Oct 2023
-
What are the advantages of ABT?07 Oct 2023
-
LED Batten Tube Lights : Everything You Need To Know16 Sep 2023
-
Special cables with HPL India15 Sep 2023
-
What is ABT Energy Meter26 Aug 2023
-
5 Benefits of Commercial LED spotlights25 Aug 2023
-
Benefits of LED Lighting in India20 Jun 2023
-
The Most Important Things You Should Know About LED Flood Lights20 Jun 2023
-
Types of Digital Meters- HPL India20 May 2023
-
MCB Switch and It’s uses - Hpl electric & power ltd20 May 2023
-
Best Electrical Modular Switches in India15 Apr 2023
-
What is Digital energy meter and how does it work?28 Mar 2023
-
All you need to know about HPL LED flood lights23 Feb 2023
-
Benefits of using Changeover Switches20 Jan 2023
-
HPL One of top 10 best electrical switches in India20 Jan 2023
-
What is a smart meter and how does it work27 Dec 2022
-
Types of electrical switches and their uses30 Nov 2022
-
Importance of Lightning in Interior Design30 Nov 2022
-
Importance of Lightning in Interior Design30 Nov 2022
-
How do Electric Meters Work15 Sep 2022
-
How To Know If Your MCB Electrical Switch Is not Working Good09 Sep 2022
-
Five Ways to Safeguard Your Home from Electrical Hazards07 Sep 2022
-
What is Grounding and Why is it Important07 Sep 2022
-
Converting Footsteps into Clean Energy19 Aug 2022
-
Four Simple Ways to Lower Your Next Electricity Bill11 Aug 2022
-
Want to know about the best Led ceiling lighting manufacturers in India10 Aug 2022
-
The best HPL 3 phase net meters in India10 Aug 2022
-
The Popularity of PVC for Wires and Instrumentation Cables05 Aug 2022
-
New Protein Produced: A Potential Solution to World Hunger04 Aug 2022
-
Electrical switches: Types and its importance12 Jul 2022
-
5 Tips To Follow When Opening An Electrical Equipment Manufacturing Company07 Jul 2022
-
Advantages of using Changeover Switch06 Jul 2022
-
Smart Meters: The Next Big Thing in Solving the Energy Crisis16 Jun 2022
-
What you need to know about the smart electric wires12 Jun 2022
-
Five Advantages that MCBs have over Fuses10 Jun 2022
-
A Potential Solution to World Hunger09 Jun 2022
-
Is it Paint or Liquid Electrical Wire09 Jun 2022
-
The Future of Modular Electrical Wiring Systems09 Jun 2022
-
Three Reasons why your Circuit Breaker keeps Tripping05 Jun 2022
-
A Guide to Reading Electricity Meter Readings05 Jun 2022
-
Top 10 Highest Electricity Consuming Countries in the World19 May 2022
-
Smart Energy Meters Will Optimise Energy Consumption in India04 May 2022
-
7 Ways to Cut Down on Your Next Electricity Bill04 May 2022
-
Difference between Smart and Analogue Meters05 Apr 2022
-
Four Ways to Raise Energy-Smart Kids05 Apr 2022
-
What you need to know about the smart electric meters05 Apr 2022
-
Signs Change your Power Sockets01 Apr 2022
-
Use MCBs and secure electrical circuits01 Apr 2022
-
Modern Electrical Accessories Paving Way to a Safer Future05 Jan 2022
-
Guide To Select The Perfect Indoor Lighting08 Jun 2021
-
Benefits of outdoor solar lightings08 Feb 2021
-
Signs your light switch is going bad08 Feb 2021
-
Lessons to choose the best modular switches and sockets08 Feb 2021
-
5 Ways to cut your household?s electric bill short12 Jan 2021
-
Why employing a structured data cabling system is so beneficial?12 Jan 2021
-
Questions to ask your electrician before hiring them12 Jan 2021
-
6 Signs that indicate a rewiring of your household is needed12 Jan 2021
-
Why solar cables instead of the regular ones?15 Jul 2020
-
Extend the life of your switchgear09 Jul 2020
-
Electrical switches: Types and its importance06 Jul 2020
-
Things to keep in mind before buying Modular Switches and Socket01 Jun 2020
-
Switch to Intelligent Switchgears01 May 2020
-
Switches and sockets that do not require attention01 Mar 2020
-
Different types of Circuit breakers01 Feb 2020
-
Industrial Wiring and its characteristics01 Feb 2020
-
Guidelines for Domestic electrical wiring01 Jan 2020
-
4 Important things about electrical wires that you may not know07 Nov 2019
-
How to avoid electric shocks during monsoon?07 Nov 2019
-
Say no to electrical shocks with quality electrical accessories07 Nov 2019
-
What you need to know about the smart electric wires03 Jun 2019
-
Best Facts About LED Lighting That Everybody Should Know03 Jun 2019